VibroBox отмечен главной наградой Smart Energy Summit 2018, прошедшем в Москве
27–28 марта 2018 года в Москве состоялся международный Smart Energy Summit 2018, участие в котором приняли свыше 400 участников. Особый акцент в программе Саммита был сделан на мировой опыт и практику выстраивания системы умной энергетики. Различные проекты и решения представлены экспертами из 15 стран мира, включая Францию, Данию, Финляндию, Великобританию, Германию, Бельгию, Голландию.
Не обошёл организатор Саммита стороной и перспективные технологические разработки, решающие задачи эффективного использования производственных активов. В формате питч-сессии представлены «молодые» проекты, цифровые решения, инновационные разработки в области энергетики, масштабируемые на промышленные производства. Десять лучших проектов из России и СНГ были оценены экспертами из акселераторов GenerationS (РВК), Сколково и VentureClub. Проект VibroBox получил наивысшую оценку и награждён специальным призом от организатора Smart Energy Summit — компании Redenex.
Компанию VibroBox на саммите представил CEO, кандидат технических наук в области цифровой обработки сигналов Игорь Давыдов.
В своем докладе Игорь рассказал о возможностях нашего свободно масштабируемого сервиса VibroBox. Автоматизация оценки технического состояния и повышение эффективности управления техническим обслуживанием оборудования — те вопросы, которые наиболее остро сейчас стоят перед высокотехнологичными предприятиями с огромными производственными фондами. Эти задачи и решает VibroBox, предлагая уникальное решение для предписываемого обслуживания (Prescriptive Maintenance).
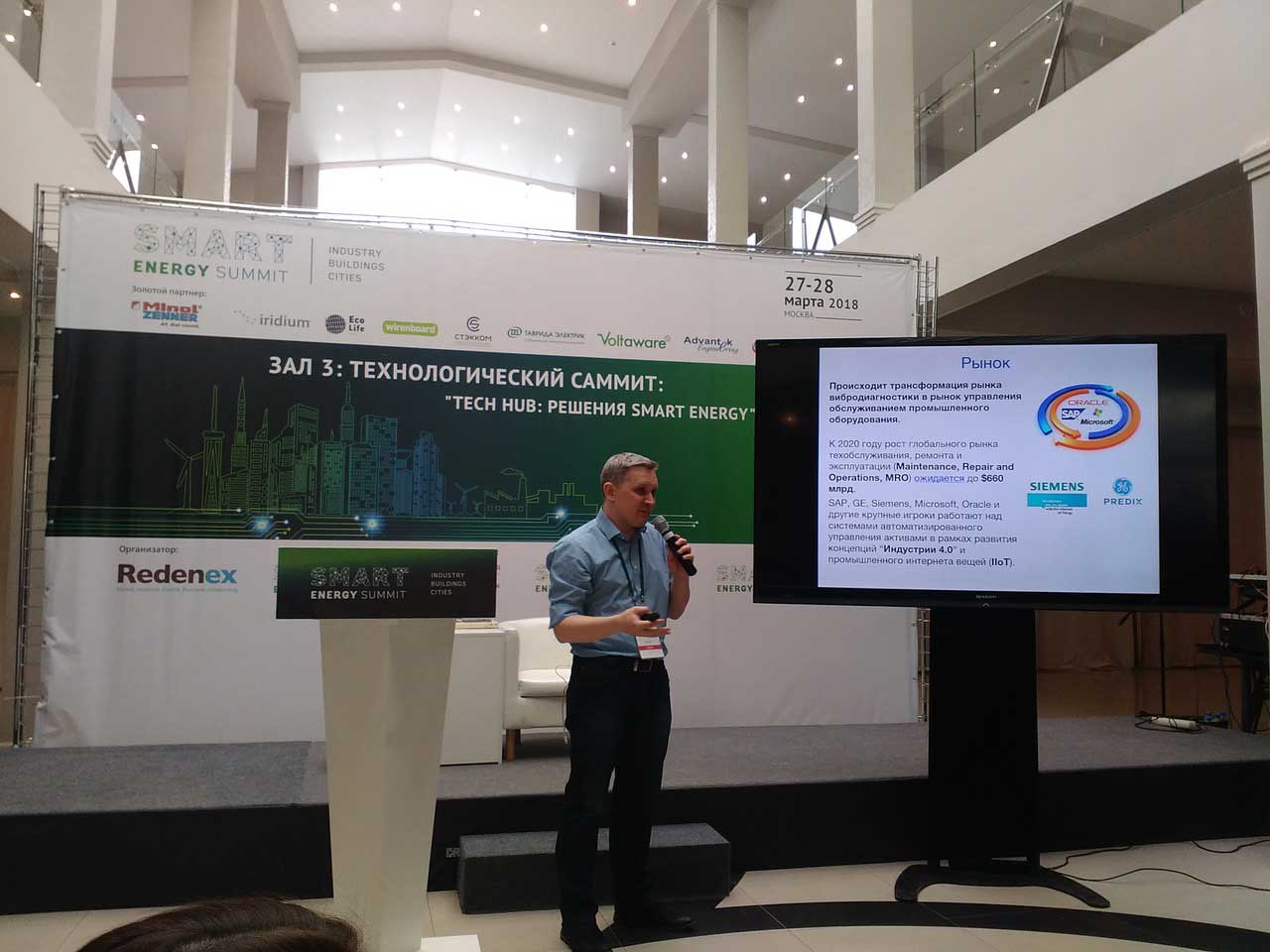
Игорь Давыдов рассказывает про сервис VibroBox.
Краткое содержание выступления CEO VibroBox Игоря Давыдова
За время эксплуатации оборудования его техническое состояние последовательно проходит ряд типовых фаз. С этими фазами напрямую связана стоимость обслуживания и ремонта.
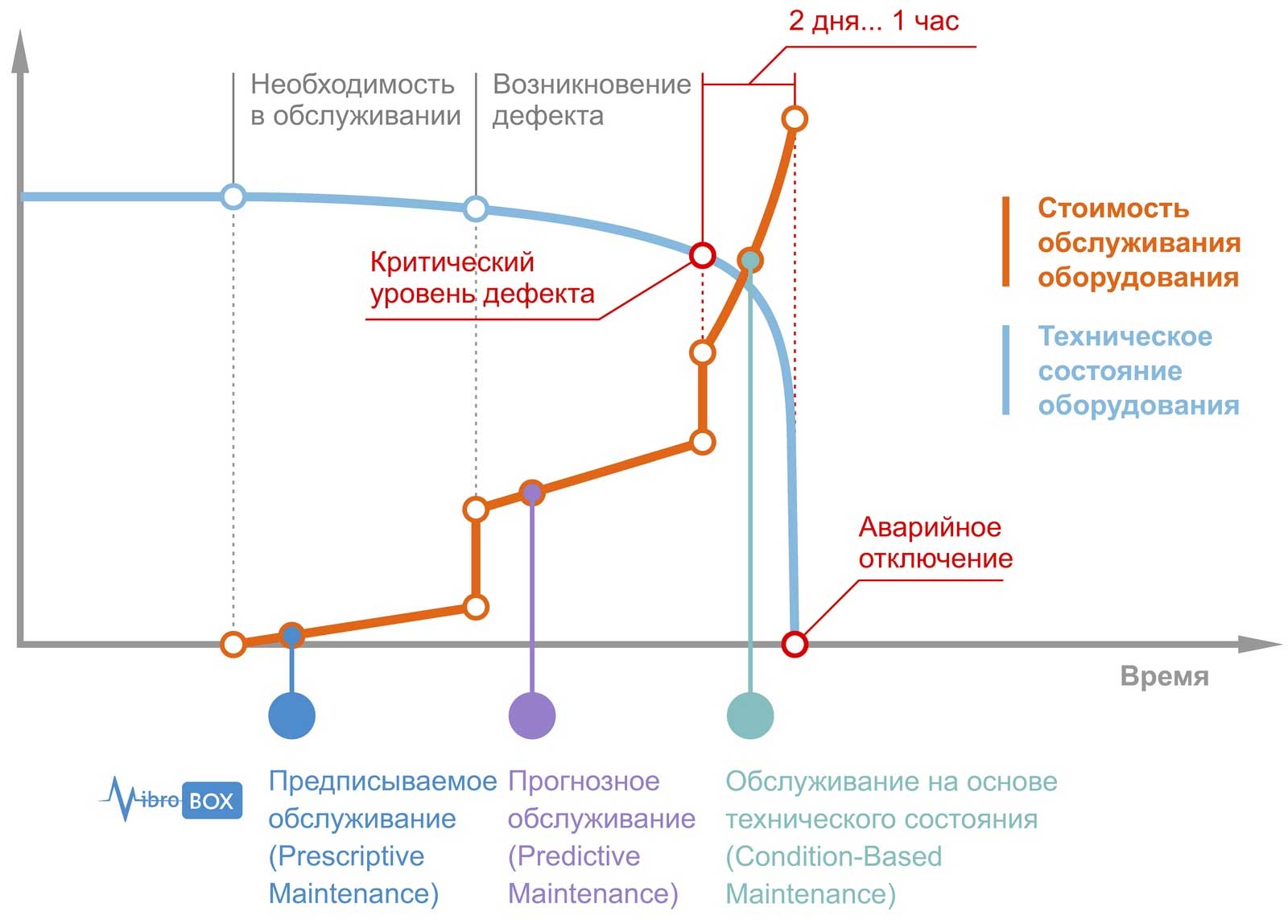
Типичные этапы деградации оборудования и технологии технического обслуживания.
В процессе эксплуатации производственным активам требуется своевременное обслуживание. Для их сохранения в отличном техническом состоянии необходимо устранять возникающие дисбаланс роторов и несоосность валов, заменять загрязнившуюся смазку и т.д. Своевременное выявление и устранение таких проблем не позволяет возникать и развиваться дефектам ответственных узлов оборудования. Игнорирование этой задачи приводит к появлению губительных условий для работы внутренних компонентов оборудования и их ускоренному деградированию, а в конечном итоге — ко внезапному и дорогостоящему ремонту. Примеры таких серьёзных дефектов — заклинивание подшипников и зубчатых передач, разрыв валов и др.
Принципиально важно выявить дефекты оборудования на самой ранней стадии. Это позволит планировать закупки запасных частей, проведение ремонтных работ без аварийной остановки оборудования и т.д. Если же проблема не была выявлена и устранена, то со временем её развитие достигнет критического уровня. При этом вырастут и температура дефектного узла, и общий уровень вибрации, а также потребление тока и другие интегральные метрики. На основе мониторинга этих метрик работают системы обслуживания оборудования по состоянию (Condition-Based Maintenance, CBM). Однако состояние дефектного узла уже не позволит уверенно прогнозировать срок его службы — он может заклинить и через час. Поэтому CBM-системы оценки технического состояния выполняют функцию аварийного отключения и позволяют лишь избежать возникновения крупных поломок, аварий и непредсказуемых последствий, связанных с техногенными катастрофами.
Системы прогностического обслуживания (Predictive Maintenance) выявляют дефекты оборудования на ранних стадиях их развития. Тем самым они дают возможность планировать техническое обслуживание, не дожидаясь перехода этих дефектов в критическую стадию. Ключевой недостаток систем Predictive Maintenance в том, что они обнаруживают имеющиеся дефекты, которые уже развиваются в оборудовании и вскоре приведут к возникновению отказа.
Наиболее перспективными являются системы предписываемого обслуживания (Prescriptive Maintenance). Эти системы призваны выявлять и устранять проблемы оборудования до того, как они приведут к появлению каких-либо дефектов. Тем самым они дают возможность:
- максимально увеличить надёжность и безопасность оборудования;
- предельно снизить затраты на его обслуживание и ремонт;
- исключить возникновение незапланированных простоев, аварий и наступление связанных с ними последствий.
В итоге с бизнеса снимаются многие риски и предельно оптимизируется ряд бизнес-процессов.
Современная практика автоматизации систем Predictive и Prescriptive Maintenance — это попытка объединить Condition Monitoring и Machine Learning. Но эта тактика не переводит обслуживание на новый уровень технической и экономической эффективности по следующим причинам:
- во-первых, в каждом конкретном случае данный подход начинает работать лишь спустя длительный период обучения нейронных сетей (недели, месяцы, и даже годы). В течение этого времени нет никаких предписаний – есть лишь обслуживание на основе данных текущей диагностики;
- во-вторых, даже если предписания появляются, сразу после изменения режимов работы оборудования либо после ремонта его компонентов обучение начинается заново;
- в-третьих, такая система принятия решений не оперирует конкретными дефектами внутренних компонентов оборудования (таких, как подшипники, валы, шестерни и т.д.). Это не позволяет контролировать его обслуживание на должном уровне эффективности.
Эти обстоятельства приводят к техническому лидерству экспертно-ориентированных систем прогностического и предписывающего обслуживания. Но вовлечение людей в процесс принятия решений существенно ограничивает применение этих систем, зачастую делая экономически нецелесообразным (особенно для небольших предприятий). Более того, воплощение концепций промышленного интернета вещей (IIoT) и Индустрии 4.0 (Industry 4.0) невозможно без полностью автоматизированных и легко масштабируемых систем управления техническим обслуживанием оборудования.
Технология VibroBox реализует концепцию предписывающего обслуживания (Prescriptive Maintenance), воплощая её в виде легко масштабируемого автоматического сервиса. Факты, определяющие ключевые преимущества VibroBox:
- при функционировании сервиса для принятия решений люди-эксперты не требуются – технология работает полностью автоматически;
- результаты диагностики включают как подробное описание дефектов конкретных деталей внутри диагностируемого оборудования, так и детальные предписания по обслуживанию — чтобы полностью исключить поломки в будущем;
- результаты диагностики доступны практически сразу (обычно через несколько дней, в некоторых случаях — через неделю), вне зависимости от типа оборудования или смены технологического процесса, и не требуют длительных предварительных исследований, сбора данных или обучения системы принятия решений.
Подробнее об итогах саммита — на информационном портале Энергетика и промышленность России.
Более подробно о технологии VibroBox можно прочитать на сайте в разделе Технология.